MEMS
Theoretical Design and Analysis of High-G Uniaxial Accelerometer
This paper details the modeling, design, analysis and fabrication of a high-g capacitive uniaxial MEMS accelerometer. Serpentine flexures transmit the motion of the proof mass in the desired sensing direction, and the motion is detected by an array of differential capacitors which reject common mode responses arising from off-axis translations. The accelerometer is designed for fabrication via surface micromachining processes. The sensitivity of the accelerometer was shown to be 7.3fF/g over a range of 0 to 200 g. Settling time of the accelerometer is 370 us, resulting in a device bandwidth of 2.7 kHz which is far below system resonance.
Course: ES227: Microfabrication Laboratory
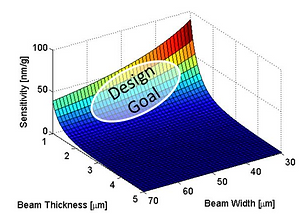
Parametric Optimization for Sensitivity

First four modes
Microfabrication of High-Quality Mesoscale Nanopositioners
This research focuses on the feasibility of using micromilling as a process for fabricating theflexural body of mesoscale nanopositioners. A desire to fabricate non-silicon microflexures formore favorable material properties and flexural responses has led MIT's Precision CompliantSystems lab to investigate the use of various metals in the design of mesoscale six-axis HexFlexnanopositioners. Micromilling is being sought as an alternative method of manufacturingHexFlex flexural bodies due to its inherent process and material flexibility. Cutting forces wereapproximated (and verified using FEM and previously-measured results) in order to selectcutting parameters that would avoid tool failure and ensure workpiece integrity. Several HexFlexdevices were successfully micromilled from various aluminum alloys. Total machining time, including setup and tool changes, was around 1.5 hours per part. The integrity of each part wasverified using optical microscopy and white-light interferometry to inspect for any microcracksor otherwise unfavorable by-products of the milling process. Ultimately, it was shown thatmicromilling is a feasible process for manufacturing low-volume to-spec mesoscalenanopositioners (±3 um) with surface roughnesses of less than 0.300 pm. Process improvementsare suggested based on observations before and during the machining process.
Course: Bachelor's Thesis (MIT)

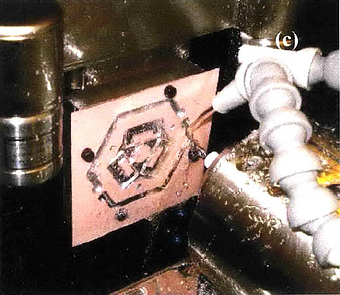
Recommended spindle speed and cutting feed as a function of tool diameter for micro-endmills
Micromilling a 6-axis HexFlex nanopositioner
Relevant Publications:
​
Non-Cleanroom Fabrication of Carbon Nanotube-Based MEMS Force and Displacement Sensors
Cullinan, M., Panas, R., Daniel, C., Gafford, J.B., Culpepper, M. (2011).
ASME 2011 International Design Engineering Technical Conferences and Computers and Information in Engineering Conference, (Vol. 6). Washington DC.
​
Design Principles and Best Practices for Rapid Prototyping of Meso- and Micro-Scale Flexures via Micromilling.
Gafford, J. B., Panas, R. M., Cullinan, M. A., & Culpepper, M. L.
Proceedings of the 2010 Annual Meeting of the American Society for Precision Engineering 25th Annual Meeting.